News & Media
NEWS
AMPO POYAM VALVES MANUFACTURES ITS LARGEST AXIAL FLOW CHECK VALVE FOR BOROUGE 4 PETROCHEMICAL COMPLEX: A 60”X64” VALVE
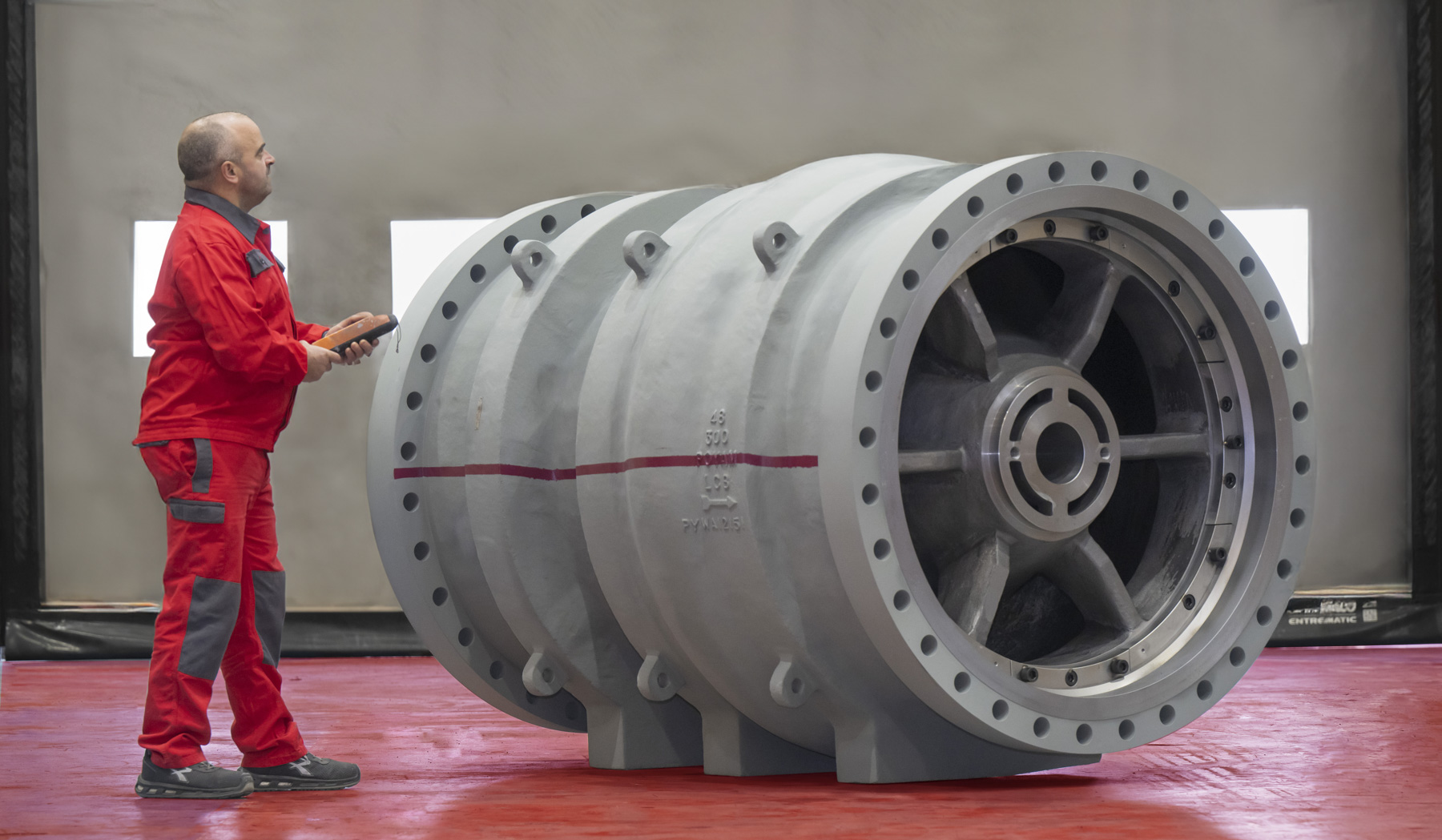
AMPO POYAM VALVES has designed and manufactured 74 highly engineered axial flow check valves for the ethane cracker unit of Borouge 4 project, a petrochemical expansion at the Borouge Complex in Ruwais, UAE, including its largest axial flow check valve ever manufactured: a 60” x 64” axial flow check valve. The project aims to increase the facility’s production capacity by 1.4 million tonnes, reaching a total of 6.4 mtpa. Borouge 4 complex will include several production units, and the primary products will be ethylene, propylene, butadiene, MTBE, 1-Butene, Pygas,1-Hexene and benzene from the new mixed-feed cracker and its derivative units. The ethylene and propylene will be converted into polyethylene and polypropylene products.
For this project, AMPO is supplying 74 cryogenic and non-cryogenic axial flow check valves, ranging in sizes from 10” to 60×64” and ratings of 150# to 1500#. The project development has involved close collaboration with Technip Energies, who is carrying out the EPC project, and with Abu Dhabi Polymers Company Ltd. (Borouge), a leading supplier of innovative plastic solutions, utilizing advanced technologies in world-class production facilities for ethylene, polyethylene, propylene, and polypropylene in the United Arab Emirates. Borouge is the owner of the petrochemical complex and a joint venture between Adnoc and Borealis.
The largest axial check valve ever manufactured by AMPO
AMPO POYAM VALVES has developed for Borouge the largest axial check valve ever manufactured by the spanish company: A 60×64” axial flow check valve. This required extensive quality control measures, including advanced simulations, pre-assembly inspections, and functional testing tailored to the valve’s size and specifications.
AMPO POYAM VALVES provided technical support in selecting the optimal valve solutions and performed detailed calculations of Cv, opening percentages, and pressure drops to ensure the highest performance and reliability for the project’s specific needs. Springs were tailor-designed for each application and materials were specifically chosen.
Unique Features and Innovations
AMPO’s axial flow check valves stand out for their advanced design, which:
- Prevents water hammer effect and ensures minimum pressure loss and a stable operation.
- Operates seamlessly in various orientations, including vertical and inclined lines, as they are not reliant on gravity for closure.
- Ensures an immediate disc reaction and a rapid self-dampening response to noticeable flow reductions, limiting backflow and valve slamming.
- Is compact and lightweight.
- Ensures zero emissions due to an absence of a bonnet or any other opening to the environment.
- Is maintenance free, providing a long service life. Due to its non-slam design, the valve is not subjected to extreme shocks associated with typical asymmetric valve designs. The valve has no soft parts, seals or o-rings which would wear, cause misalignment or need replacing. And the metal-to-metal disc seat seal achieves tight shut-off with 100% reliability.
With the achievement of this new milestone, AMPO strengths its presence in the petrochemical industry and expects to continue contributing to the success of large-scale, demanding projects like Borouge 4, reaffirming its position as a worldwide leader in highly engineered valves for the most severe services.